How to Choose the Right Cork Rubber Sheet Thickness for Industrial Gaskets and Flooring Applications
Thickness Matters, But Why?
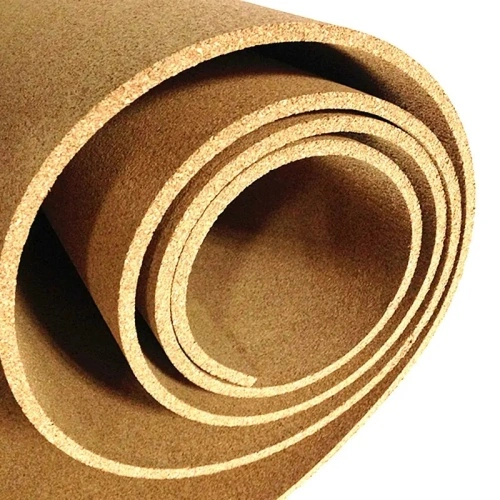
How to Choose the Right Cork Rubber Sheet Thickness
Let’s get real: thickness isn’t just a number on a spec sheet—it’s the difference between a gasket that leaks like a sieve and one that outlives your machinery. Cork rubber sheets thrive on their cellular structure, but slap on the wrong thickness, and you’re basically throwing money into a thermal vortex.
The Pressure Paradox
For industrial gaskets, thickness is dictated by pressure, not hope. A 3mm sheet might work for low-pressure pipe joints in a brewery, but try that in a hydraulic press system, and you’ll watch it compress like overcooked noodles. I’ve seen 6mm sheets save a chemical plant’s valve assembly from catastrophic failure at 150 psi. Yet, go thicker than 8mm, and you risk compromising flexibility—critical for sealing irregular surfaces.
Flooring: Where Thickness Meets Traffic
Flooring applications are a battlefield of boots, forklifts, and dropped tools. A 5mm cork rubber sheet in a warehouse aisle? That’s a rookie mistake. After six months, it’ll look like the surface of the moon. Bump it to 8mm with a dense rubber blend, and suddenly, impact resistance triples. A German auto factory I advised reduced floor-related downtime by 40% after upgrading to 10mm sheets—thick enough to dampen vibrations from robotic arms, thin enough to avoid tripping hazards.
The Cost-Thickness Tango
Here’s the dirty secret: thicker isn’t always better. A 12mm sheet might scream “premium,” but if your flooring application only handles light foot traffic, you’re overengineering and overspending. I once audited a textile mill using 15mm sheets beneath looms—absurd overkill. Switching to layered 6mm + 4mm composites saved them 22% material costs without sacrificing noise reduction.
My Unpopular Opinion
The industry obsesses over standardized thickness charts, but real-world performance demands customization. Mix 4mm cork rubber with a 2mm neoprene underlayer for acidic environments, or stagger thickness zones in flooring for heavy machinery pathways. Stop treating thickness as a standalone metric—it’s a dance partner with density, temperature, and human error.
Final Word: Test, Don’t Guess
Slap samples in your actual environment. Bake a 5mm gasket at your operating temperature. Drive a forklift over that 8mm flooring prototype. Data beats dogma every time. Your ideal thickness isn’t in a catalog—it’s hiding in the chaos of your workshop.